- November 28, 2023
- Posted by: Uma Raj
- Category: Industries
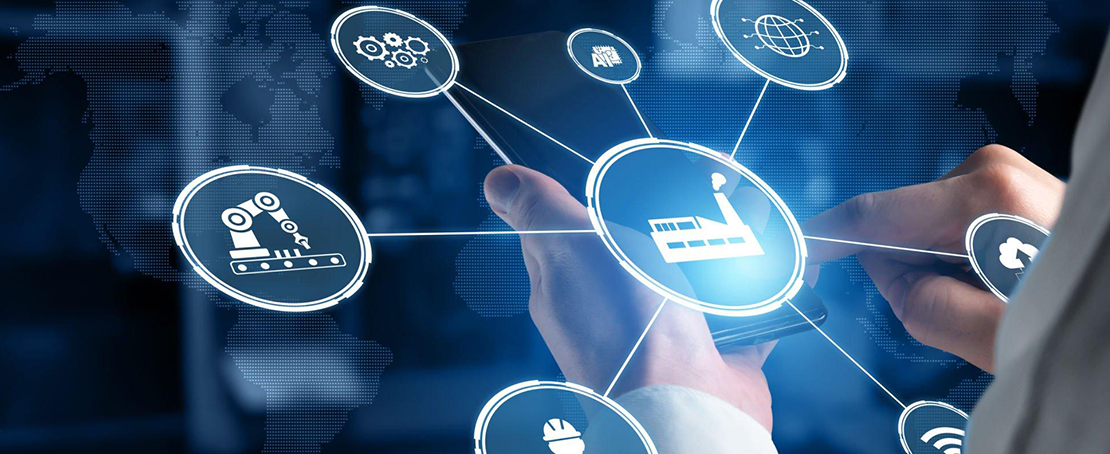
Unifying information and operational technologies: Bridging the gap
In advanced industrial settings, two primary components are prevalent: automated communication systems and physical assets. These components span several layers—from the factory floor to the cloud—connecting devices, equipment, controllers, monitors, networks, and systems. IT/OT integration is often emphasized in the context of industry 4.0, and for a good reason. IT/OT convergence is the foundation for modern businesses, facilitating transformation and growth while enabling automation and innovation across various business domains. Although IT and OT are two independent, robust systems, their convergence drives transformation in every aspect of business.
IT/OT integration signifies merging information technology (IT) and operational technologies (OT). IT/OT convergence is not merely about organizational structural changes or an excessive focus on technology; it encapsulates a comprehensive change often called “digital transformation.”
While IT systems primarily deal with communication and data management, OT systems encompass physical devices responsible for executing tasks on the shop floor. The subsequent layer in OT systems incorporates real-time monitoring software, ensuring optimal performance of physical devices and identifying deviations from the desired operational conditions.
Perspectives in IT/OT integration: Beginners, veterans, and leaders in industry transformation
IT/OT convergence represents a significant paradigm shift that introduces various challenges, affecting newcomers and established players. The planning phase may daunt beginners, while those already involved in the IoT/IIoT space grapple with integrating new devices, technologies, and specifications into existing processes. Conversely, leaders face continuous pressure to deliver intelligent innovations with rapidly evolving technologies to remain competitive.
Converging IT-OT systems may seem easy, but there are significant differences in how various organizational departments perceive them. For instance, shop-floor personnel prioritize efficiently functioning and maintaining devices or equipment, while the IT crew aims to connect assets with respective software and networks. Operations teams assess the business benefits of IT/OT collaboration.
Ready to unlock the potential of IT-OT integration for your business? We’ll analyze your unique needs, assess your current infrastructure, and develop a customized strategy to merge your information and operational technologies seamlessly.
Common challenges associated with IT/OT integration
Different department perspectives: Individuals or teams—are often focused on their routine tasks, making collaboration efforts appear as intrusions from other departments, impacting their primary objectives.
Ambiguity and lack of clarity: Although industry 4.0 offers significant potential, decision-makers may need a more precise understanding, hindering confident decision-making.
Legacy products inventory: Many industrial sites use devices from diverse vendors to meet evolving business requirements. When the personnel who initially deployed these devices are no longer available, transitioning legacy devices can be complex.
Absence of expert guidance: IIoT implementation demands significant efforts in terms of both business and technology. Additionally, investments in new infrastructure, tools, and processes can take time and effort.
Other operational challenges—such as interoperability, scalability, remote operations, network security, and cloud compatibility—can slow the adoption of IT/OT integration. Overcoming these challenges often involves training, collaborations, practical experiments, gradual technology adoption, and partnership models facilitating a seamless transition toward industry 4.0 goals.
Steps for a successful IT/OT integration strategy and key technologies:
Companies employ various IT/OT integration approaches based on their unique priorities, resources, and budgets. However, there are a few steps to implement an effective IT/OT strategy:
- 1.Identify the need: Understanding the need for IT/OT convergence is the first step for newcomers embarking on the industry 4.0 journey. Large manufacturers may focus on self-corrective processes and automation driven by interconnected device’s real-time data.
- 2. Set priorities: As companies grow, their preferences align with short and long-term business objectives. A clear vision regarding tools, technologies, and processes is crucial for IT/OT maturity.
- 3. Identify the right partner: Given the extensive IIoT landscape, organizations often seek industry partners who can serve as advisors and business consultants, guiding them through their Industry 4.0 journey.
- 4. Plan risk mitigation: Given the substantial investments and long implementation cycles, contingency plans are only sometimes ideal for IT/OT strategies. However, staying informed about market trends and making well-informed decisions can minimize the impact of unforeseen circumstances.
Wondering where to start with IT-OT integration? Stay tuned to our upcoming eBook to learn your obstacles and how to overcome them with our IT-OT integration best practices.
Amidst the hype surrounding IT/OT technology, scalability is one critical factor for the present and the future. The ability to scale IT/OT communication architecture in industrial manufacturing hinges on three pivotal factors: field assessment, requirement analysis, and plant design and infrastructure.
Field assessment
- Field assessment comprehensively evaluates the existing physical infrastructure and conditions within the industrial environment. It includes examining the shop floor, manufacturing facilities, and the various devices and equipment.
- This assessment aims to understand the manufacturing setup’s current operational technologies (OT). It looks at how devices and machinery are connected, the types of sensors and control systems in place, and these assets’ overall condition and reliability.
- The assessment helps identify any existing limitations, challenges, or bottlenecks in the OT systems that may hinder the integration of information technology (IT) systems. It provides a baseline understanding of the on-ground infrastructure and its IT/OT convergence readiness.
Requirement analysis
- Requirement analysis carefully examines the specific needs and objectives of the manufacturing operation. It considers what the organization aims to achieve through IT/OT integration.
- This phase typically includes discussions with stakeholders, including operations teams, IT teams, and business leaders, to understand their goals and expectations. It also considers regulatory and compliance requirements that may impact the integration.
- Requirement analysis helps define the functionalities and capabilities the IT/OT communication architecture must support. For instance, it may involve determining the need for real-time data monitoring, predictive maintenance, or remote operations.
- By aligning the IT/OT integration strategy with the operational requirements, an organization can ensure that the technology investments serve the intended business objectives.
Plant design and infrastructure
- Plant design and infrastructure encompass the physical layout and setup of the manufacturing facility. It involves equipment arrangement, network cabling, and power distribution.
- The infrastructure must be designed or adapted to support the IT/OT integration. This includes ensuring that the network can handle the increased data traffic, reliable power sources, and adequate provisions for connecting IT devices to the plant’s machinery.
- Additionally, infrastructure design may need to accommodate the installation of new sensors, controllers, or other IT components to enable the flow of data and control signals between IT and OT systems.
- This factor also considers the scalability of the physical infrastructure and whether it can support future expansion and technology upgrades as the organization’s needs evolve.
Several key activities directly impact the success of future-proof strategies for IT/OT integration:
- Network architecture evaluation and preparation
- Inventory of software/components
- Security and compliance assessment
- Interplant and multi-geography connectivity
- Disaster recovery planning
- Data communication strategies
- Troubleshooting protocols
- Analytics and reporting mechanisms
It is crucial to understand that the success of IT/OT collaboration is not just dependent on technology. Manufacturers should acknowledge that while automation is significant, human intelligence remains vital. The ongoing investment in individuals, policies, and procedures is indispensable for realizing the promising future envisioned through IT/OT integration.
The future of manufacturing and the evolution of IT/OT integration
Intelligent factories are already underway, marked by extensive data consumption from interconnected systems, devices, machines, and applications. These smart factories will exhibit deep interconnectivity empowered by automation, artificial intelligence (AI), machine learning (ML), and remote operation—fostering efficiency, effectiveness, and safety in production.
At the core of this revolution lies digital transformation, where intelligent factories of the future envision human involvement predominantly at the supervisory level. AI-driven collaborative robots will conduct most shop-floor tasks.
The evolution of IT/OT integration in the future will be guided by three fundamental principles of automation: connection, collaboration, and innovation. IT/OT connectivity will adapt to demand, identifying and swiftly adopting the most optimized approach to fulfill specific objectives.
Discover how our comprehensive IT-OT integration solutions and best practices enhance your industry’s efficiency, productivity, and innovation.